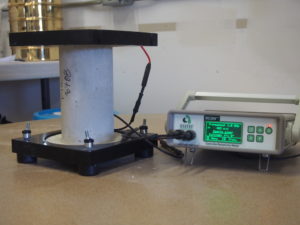
Throughout my career, our industry has been pursuing performance specifications for concrete. That is, we want specifications for what the concrete must do, not what it must be. The sticking point has always been which tests accurately predict durability while also being both rapid and repeatable. In other words, how do we specify tests for durable concrete?
Durability is difficult to test for. Unlike compressive strength, it’s not intrinsic to concrete. Rather, it depends on the service environment. The American Concrete Institute building code (ACI 318-19) incorporates concrete exposure classes to characterize the environment in terms of freeze-thaw cycles, sulfate, water, and corrosion.
For many years, state highway officials have asked for what they call “coffee can tests”—simple, rugged tests a technician can conduct quickly in the field. Such tests exist, but they’re generally neither reliable nor meaningful. Let’s consider what we need in a test method—accurate prediction, speed, and repeatability—and the tradeoffs we have to make.
Accurate prediction v. speed
Ideally, tests for durable concrete would accurately predict durability. To do that, they need to simulate field conditions, or at least induce the same failure mode. But the nature of durability is that it takes a long time to see results. If a concrete is durable in a particular environment, it will last a long time in a test that simulates that environment.
To speed up the test, we can alter the conditions in various ways. For example, we can raise the temperature to accelerate chemical reactions. ASTM C1293 uses this strategy to accelerate the alkali-silica reaction in concrete prisms. Even so, it takes a year to determine whether an aggregate is susceptible to expansions, and two years to verify mitigation measures.
Another strategy is to expose more surface to reaction. ASTM C1260 and 1567 require crushing coarse aggregate to a specified size grading. They also raise the temperature and increase the concentration of alkalis. Both tests include two weeks of exposure, and both are conservative. That is, they will fail some aggregates (C1260) or material combinations (C1567) that could perform acceptably in service rather than pass some that wouldn’t perform well.
Unfortunately, the things we do to accelerate testing may induce a different failure mode than what occurs in the field. That makes it difficult to correlate the test with field performance. We could end up with concrete that doesn’t do well in the test but is okay in the field. Usually that means we end up spending more for a concrete that passes the test—a waste of resources. Worse still, we could end up with concretes that pass the test but perform poorly in the field. The ideal test is conservative but not too conservative.
Speed v. repeatability
There’s also a tradeoff between speed and repeatability. That is, if two technicians conduct the same test on the same concrete, they should get substantially the same result. But simple, quick tests such as the “coffee can” tests can also be highly variable. So the same concrete could pass the test or not, depending on who conducts it.
If an acceptance test is too variable, the supplier must mitigate the producer’s risk of rejecting good concrete. That is, the concrete must be much better than specified so it will pass the test no matter what. As with overly conservative tests, highly variable tests needlessly increase the cost of the concrete and waste resources.
Highly variable tests also increase the likelihood and cost of disputes. Suppose the concrete is rejected on the basis of ASTM C1202 at age 28 days. If the engineer of record requires removal and replacement of this concrete—along with any concrete that overlies it—there will be a dispute. With such a variable test, a second test of the same concrete may give a passing result. So which result is right? And who bears the cost of removing and replacing the concrete, along with the penalties for delays? We do have better tests, but they’re less familiar. Often that means we don’t know what limits to specify.
Different tests for different purposes
In research, accurate simulation of field performance is more important than anything else. Ultimately, tests for durable concrete in a research setting will shed light on how failure occurs in service. That’s the only way to understand what’s happening, prevent or manage it, and predict service life. This kind of simulation can take years or even decades.
We can use computer modeling to simulate failure mechanisms. Once we’ve built the model, it can save a lot of time by trying out a wide range of “what ifs”. But for the model to be any good, it needs good input data. That is, simulation of the actual mechanisms with accurate control or monitoring of the variables is essential. This is painstaking and lengthy work, but once you have a good data set you can keep using it for updates of your model.
Such long-term tests aren’t practical for quality control within the time frames of most construction projects. However, 1- or 2-year tests may be feasible for qualifying concrete mixtures. For a posttensioned bridge with a design life of 75 or 100 years, it may make sense to conduct creep testing for a year. You can also test a suite of proposed concrete mixtures simultaneously. That way if some of them don’t work, you still have some options available.
State highway departments may test aggregates for alkali-silica reactivity because it costs less than removing and replacing miles of pavement. They may even test them with commonly available cementitious materials so they know how best to control the reactivity. Considering that the full verification protocol can take 3 years, it’s suitable only for prequalification of materials and combinations.
Similarly, admixture suppliers may test their admixtures with the materials in their market so they know what works with what. So long as the materials don’t change, they can use the test data for multiple projects.
Quality control tests for durable concrete
For quality control, the ideal test is quick, simple, repeatable, and correlated to long-term performance. Usually we have to settle for quick and simple. But we can correlate some quick, simple tests with longer-term tests during qualification. For example, ASTM C1074, “Standard Practice for Estimating Concrete Strength by the Maturity Method,” helps us predict the strength from the temperature history. That way we can safely remove the forms or posttension the concrete, knowing exactly when it’s strong enough. We can also use the temperature history with thermal modeling to manage thermal stresses.
Field tests can help ensure that the concrete is essentially the same as the specified mixture. For example, AASHTO T 318, “Standard Method of Test for Water Content of Freshly Mixed Concrete Using Microwave Oven Drying” verifies the water-cementitious materials ratio. And ASTM C231 measures the air content.
Because ours is a litigious society, it’s helpful to retain samples just in case. A 5-gallon pail of each aggregate and each cementitious material used on the job won’t take up much space, but could prove invaluable if there’s ever a question of what went wrong. And an extra cylinder of the as-delivered concrete takes only a few minutes to make, but can help answer that same question. These simple measures may even save us the trouble of coring the in-place concrete.
Setting the priorities
You can’t always get what you want
But if you try sometimes, well, you just might find
You get what you need—Mick Jagger and Keith Richards
In testing we can’t get everything we want, but we can set priorities so we get (most of) what we need. To understand the mechanisms of failure and develop accurate models, we need painstaking methods that take a long time to produce results. To evaluate materials and combinations of materials, we may need some 1- or 2-year tests. With proper planning, we can fit them into the schedule. We can also correlate them with the quick, simple tests we use in the field. That way we can be confident that we’ll have the durability we need.