Concrete exposure classes are part of a decades-long trend toward performance specifications. Traditionally, specifications were prescriptive. That is, they specified what the concrete must be. So there might be limits on the water-cementitious materials ratio, the cement content, or the type of cement to use. Performance specifications spell out what the concrete must do. For example, for concrete subject to deicing salts, there might be limits on the charge passed according to ASTM C1202. In practice, specifications have long included both performance- and prescriptive requirements.
The American Concrete Institute adopted concrete exposure classes beginning with the 2008 version of its Building Code Requirements for Structural Concrete, more commonly known as ACI 318. If you need to specify durable concrete, Beton can help.
What are concrete exposure classes?
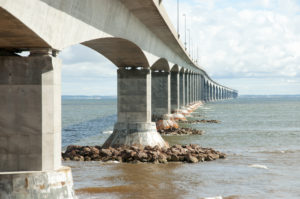
The service environment for a concrete structure or pavement may pose challenges to its durability. ACI 318 categorizes them as freeze-thaw (F), sulfate (S), water (W), and corrosion (C). Each category has numerical rankings for severity. For example, an exposure class of S3 indicates the severest exposure to sulfates, such as for a concrete foundation in soil with a high sulfate concentration. On the other hand, an F1 exposure would entail cycles of freezing and thawing with only limited contact with water.
Exposure classes are not mutually exclusive
It’s important to recognize that the service environment may include more than one type of exposure. For example, a parking garage slab may experience freezing and thawing in the presence of water and deicing salts. This is both an F3 and a C3 exposure, so you need to design for both conditions.
On the other hand, while seawater contains appreciable concentrations of both chlorides and sulfates, chlorides mitigate the effects of sulfates. So a bridge pier in seawater has both a C3 and an S1 (not S3) exposure. Strangely enough, sulfate-resistant cements are less resistant to chlorides than regular cements. The aluminates that make concrete vulnerable to sulfate attack also keep chlorides from penetrating easily into the concrete.
ACI 318 doesn’t cover all possible exposure conditions. Concrete in industrial or agricultural environments may experience various kinds of chemical or physical attacks. If you’re working with that kind of application, you need to find out exactly what’s in the environment and design for all of it. Also, if you have an aggregate that’s susceptible to alkali-silica reaction, you need to verify that you have enough of the right fly ash, slag cement, and/or silica fume to control the expansions. ASTM C1778 provides guidance for that.
Freeze-thaw exposure (F)
Cycles of freezing and thawing can be destructive to concrete because water expands on freezing. There is always some water in concrete. Water is one of the ingredients, and water can infiltrate from the environment into the concrete. We have two ways of preventing freeze-thaw deterioration: keep the water out and make room for freezing water to expand.
The severity of freeze-thaw exposure ranges from F0 (no exposure) through F1 (freezing and thawing with limited exposure to water) and F2 (frequent exposure to water) to F3 (freezing and thawing with exposure to water and deicing chemicals).
For F0 there are no particular requirements for the concrete. As the severity increases, the maximum limit on water/cementitious materials ratio goes down and the required air content goes up. If you’re placing the concrete in hot weather, you need to pay special attention to the air-void system to get good results. The water/cementitious materials ratio largely determines the permeability of the concrete. The lower the permeability, the less easily water can get in. A system of well-distributed, fine air bubbles gives the water a place to expand.
In addition, concrete with too much supplementary cementitious material (SCM) may be susceptible to salt scaling. So for F3 exposure, ACI 318 also imposes maximum limits on how much of each you can use.
However, scaling is often related to finishing and curing procedures, and timing can make a difference. If you need to use more SCM to meet other requirements, you can limit scaling via a performance criterion. For example, you could specify a maximum limit of 2 for the visual rating as determined by ASTM C672.
Sulfate exposure (S)
Sulfates in water or soil can react with the aluminate compounds in hydrated cement, producing first ettringite and then gypsum. As engineers have known since the early 1900s, sulfate-bearing soils are prevalent in the western US and Canada. ACI 318 defines four exposure classes for sulfates in terms of both water-soluble sulfate in soil and dissolved sulfate in water. To determine just how severe the sulfate exposure is, analyze the soil in accordance with ASTM C1580.
ACI 318 imposes maximum limits on the water/cementitious materials ratio to limit the rate at which soluble sulfates can migrate into the concrete. In addition, it allows only certain types or combinations of cementitious materials. That is, increasing severity of sulfate exposure calls for more sulfate-resistant cementitious materials. You can use Type V (sulfate-resistant) cement if it is available. If not, combinations of portland cement with appropriate proportions and kinds of fly ash and/or slag cement are acceptable.
If you prefer a performance specification, you can require that the combination of cementitious materials meet the criteria of ASTM C1012, “Standard Test Method for Length Change of Hydraulic-Cement Mortars Exposed to a Sulfate Solution.”
It’s important to note that no cementitious materials are completely sulfate-proof. That’s why you need to limit the water/cementitious materials ratio so that sulfate attack is confined to the surface of the concrete. There will still be deterioration, but you can achieve the desired service life. For complete protection against sulfate attack, you need a protective barrier.
Water exposure (W)
Concrete that must have low permeability to water has a water exposure class W1. It’s required to have a water/cementitious materials ratio less than or equal to 0.50.
However, if permeability matters it’s important to understand what kind of permeability you care about. In a water-retaining structure such as a water tank, you have to control cracking. So you may want to specify a limit on shrinkage as well as water/cementitious materials ratio. Be aware that too low a water/cementitious materials ratio may result in greater shrinkage and cracking. Also, structural design and detailing are extremely important. If there’s too much restraint of shrinkage, you’ll have significant cracking.
People often refer to ASTM C1202 as the “rapid chloride permeability test.” This is a misnomer in more ways than one. Strictly speaking, permeability refers to the movement of fluids through a material. So you can have water permeability or air permeability, for example. But migration of ions is by diffusion, so it’s chloride diffusivity, not chloride permeability. Remember: ions swim; they don’t fly. Also, the test doesn’t directly measure chloride migration, which takes far too long for practical purposes. Instead, it measures the electrical charge passed during the six-hour period of the test.
If you’re concerned about water permeability, stick with tests or prescriptive criteria that relate more directly to that. For example, you might use the ring test (AASHTO T334) as a means of limiting the tendency for the concrete to crack under restraint.
Corrosion exposure class (C)
ACI 318’s corrosion exposure classes comprise C0 (concrete dry or protected from moisture), C1 (concrete exposed to moisture but not to an external source of chlorides), and C2 (concrete exposed to moisture and an external source of chlorides). Sources of chlorides include seawater, brackish water, deicing salts, or spray from any of these sources. Because corrosion rates are much higher in the presence of oxygen, concrete that is completely submerged in seawater is much less vulnerable than concrete in the tidal- or splash zones, where both water and oxygen are abundant.
Concrete subject to exposure class C2 must have a water/cementitious materials ratio no higher than 0.40. In addition, ACI 318 specifies minimum cover over the reinforcing bars.
Alternatively, you may want to specify a maximum limit of, say, 1000 coulombs charge passed in accordance with ASTM C1202. Because cracked concrete is of little use in protecting reinforcement from corrosion, AASHTO T334 may also be helpful in qualifying concrete mixture proportions.
Designing for durability
As you can see, specifying a durable concrete is not a simple “cookbook” procedure. You must take into account all of the exposure conditions, some of which may interact with others. There is often more than one way to accomplish the desired result. By using performance requirements wherever you can, you allow the contractor to select the most economical one. You can go a long way toward durability to most concrete exposure classes by limiting permeability, as that limits any destructive reactions to the near-surface concrete.
Concrete exposure classes address concrete mixture proportioning. However, good concrete takes more that just a good “recipe”. You also need to pay attention to proper batching, mixing, transport, placement, finishing, and curing. In addition, structural design and detailing can help by getting water off the surface quickly so it doesn’t migrate in, or by minimizing cracking. Service life prediction can help you evaluate the costs and benefits of various means of achieving durability.
It’s worth noting that if you’re placing concrete in hot weather or cold weather, you need to take special precautions to maintain its durability. The concrete could reach the specified strength under these conditions without developing the necessary internal structure.