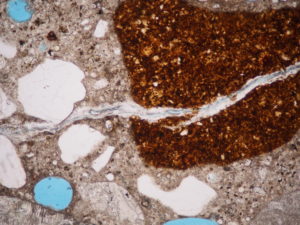
ASTM C1778, “Standard Guide for Reducing the Risk of Deleterious Alkali-Aggregate Reaction in Concrete,” can help you decide how best to mitigate expansions due to reactive aggregates. It covers both alkali-silicate and alkali-carbonate reactive aggregates. Both reactions result in expansion and cracking of the concrete.
We’ve discussed “classic” alkali-silica reaction, by far the more common of the two, in a previous blog. It involves aggregates containing reactive forms of silica such as opal, strained quartz, or volcanic glass. Fly ash, slag cement, silica fume, and natural pozzolans can all help to control the expansions. Using one or more of these materials, you should be able to design a concrete mixture that meets your requirements.
Alkali-carbonate reaction involves dolomitic aggregates. Alkali-carbonate reaction is rare, but unlike alkali-silica reaction it can’t be mitigated. That is, the only option is not to use susceptible aggregates. ASTM C1778 shows you how to identify them so you can avoid them.
There are no proven measures for effectively preventing damaging expansion with alkali carbonate reactive rocks in concrete and such materials need to be avoided.—ASTM C1778.
Using ASTM C1778 to evaluate field performance of aggregates
ASTM C1778 contains a flow chart which shows how to evaluate the potential reactivity of an aggregate. The first step is to evaluate the field performance of the aggregate in concrete. Find as many structures as you can that incorporate the same aggregate. They should be at least 15 years old, as the tell-tale expansions and three-armed cracks take about 10 years to develop. Get as much information as you can about the cementitious materials in each concrete, particularly the alkali loading. You also need to know about any exposure of the concrete to moisture and deicing salts. Obtain cores from these structures to examine petrographically using ASTM C856.
If the aggregate has not been reactive under these conditions, you may use it in concrete so long as the exposure conditions aren’t any more severe than in the existing structures. It’s important to make sure that the aggregate source hasn’t changed. Also, your concrete should have at least as much of the appropriate supplementary cementitious materials as the existing concrete. In addition, the alkali loading of your concrete shouldn’t be any higher.
As you can imagine, it may be difficult or impossible to obtain sufficient long-term data on the field performance of your aggregate. If that’s the case, you’ll need to evaluate it in the laboratory.
Using ASTM C1778 to assess potential for expansion
Petrographic examination (ASTM C295) will identify potentially reactive constituent minerals. For alkali-silica reaction, these include opal, chert, chalcedony, cristobalite, tridymite, strained- and microcrystalline quartz, and volcanic glass.
A microtexture of dolomite rhombs in a fine-grained matrix of calcite, quartz, and clay is characteristic of alkali-carbonate reactive aggregates. However, not all such aggregates exhibit this microtexture. The chemical composition can give further information. For this purpose, use a Canadian test, CSA A23.2-26A, “Determination of Potential Alkali-Carbonate Reactivity of Quarried Carbonate Rocks by Chemical Composition”. The relationship among the lime- (CaO), magnesia- (MgO), and alumina (Al2O3) contents indicates its potential for alkali-carbonate reactivity.
If the aggregate is potentially expansive, you need further testing to evaluate the severity of the reaction.
Laboratory testing of expansion
If petrography indicates potential alkali-silica reactivity, test for expansion using ASTM C1260 (mortar bar test). This test is rapid but can give false positives. That is, it may result in rejection of acceptable aggregates. If the expansion is less than 0.10% after 14 days’ exposure, you may consider the aggregate to be innocuous. If it’s 0.10% or more, it’s potentially deleterious in the absence of mitigation measures. Although it’s fairly common for aggregates that fail the mortar bar test to pass the concrete prism test, some aggregates pass the mortar bar test and fail the concrete prism test. So don’t accept or reject an aggregate solely on the basis of the mortar bar test. Instead, conduct further testing using ASTM C1293.
ASTM C1293, the concrete prism test, can be used to test both alkali-silica and alkali-carbonate reactive aggregates. An expansion of less than 0.04% after 1 year of exposure indicates that the aggregate is innocuous. If the expansion is 0.04% or more, a petrographer should examine the specimens for alkali-carbonate reactive aggregates. It’s possible to mitigate expansions due to alkali-silica reaction, but not those due to alkali-carbonate reaction. Some aggregates are susceptible to both, so it’s important to know the mineral composition of the aggregates. A petrographer with expertise in evaluating alkali-carbonate expansions should make these determinations.
Another test, ASTM C1105, can help you determine whether the aggregate is susceptible to deleterious alkali-carbonate expansions. Expansions of 0.025% or greater at 6 months or 0.030% at 12 months indicate that the aggregate is not suitable to use in concrete. If the expansions are below these limits, you still need to test the aggregate for potential alkali-silica reactivity.
Mitigation measures
ASTM C1778 also indicates how to evaluate potential mitigation measures. 1567, which is similar to ASTM C1260 in procedure and duration, is suitable when the results for ASTM C1260 and ASTM C1293 are within a certain range (Zone 2). When the results for ASTM C1293 are high relative to those for ASTM C1260 (Zone 3), you’ll need to evaluate mitigation measures using ASTM C1293 for 2 years’ exposure. For some aggregates, ASTM C1567 may indicate good results for mixtures that will not perform well in service. ASTM C1778 categorizes these in Zone 1.
Some agencies specify longer exposure periods for ASTM C1567 with the same 0.10% expansion limit. These criteria do not correlate well with either ASTM C1293 or field performance. Thus the engineer could end up specifying more supplementary cementitious materials than necessary and have difficulty meeting other performance criteria.
We’ve discussed balancing accuracy, speed, and repeatability of testing in a previous blog. Evaluating aggregate takes more than 1 year and evaluating mitigation measures could take another two. The concrete prism test doesn’t fit well with construction schedules, so qualify the aggregate source ahead of time. When evaluating mitigation measures, it’s a good idea to develop multiple mixtures simultaneously. That is, don’t bet on just one and wait for the results before you try another.
Conducting multiple trials in parallel is especially important when material supplies aren’t completely reliable. Suppose the fly ash you’re using becomes unavailable when the utility shuts down its power plant for maintenance. Or high demand makes it hard to get slag cement. Having data on multiple mixtures allows you to make changes seamlessly. The initial testing costs will be higher, but you can confidently adjust to changing conditions without delay. For large or multi-year projects, that flexibility is well worth the cost.
Different measures for different applications
ASTM C1778 also provides guidance for evaluating both the risk and the potential consequences of deleterious expansions. Table 2 uses the exposure conditions and the class of aggregate to rate the risk. Non-massive concrete in a dry environment has the least risk due to exposure, while mass concrete, humidity, and exposure to alkalis increase the risk. In addition, the more reactive the aggregate (from the results of the mortar bar and concrete prism tests) the greater the risk.
Table 3 classifies the severity of the consequences of alkali-silica expansions in terms of the safety, economic, and environmental aspects. For example, for a non-bearing element in a building, the consequences of alkali-silica expansion aren’t significant. However, the economic costs of replacing a severely cracked highway pavement before its time are less acceptable. And for a dam, a bridge, or a nuclear facility, the safety and economic consequences would be unacceptable. Also, the longer the design service life the more severe the consequences of a premature failure.
From the classification of the structure and the risk, you can determine the minimum amounts of the various supplementary cementitious materials to use. In some cases you’ll also need to limit the alkali loading of the concrete.
Unfortunately the procedures in ASTM C1778 are neither straightforward nor rapid. However, making safe use of the available materials requires this sort of nuance. Aggregate suppliers and state highway departments have an interest in obtaining the necessary data ahead of time, so they can be good sources of information for your project. But you’ll still need good planning to make sure you’ve dotted all the i’s and crossed all the t’s.