Elevated temperatures affect the mixing, placement, and finishing of fresh concrete. In our blogs about mass concrete and hot-weather concreting, we’ve alluded to what happens when concrete cures at elevated temperatures. Now let’s take a look at the materials science behind it.
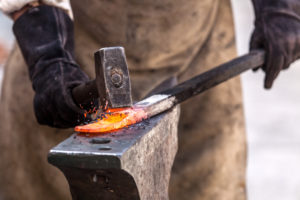
Materials science is all about the structure-property relationship. That is, you can change certain properties of a material by changing its microstructure. A swordsmith who wants steel that holds its sharp edge has to make many fine layers of carbon and iron. That takes many iterations of pounding and folding over and tempering to produce the right microstructure.
Microstructure and strength
The microstructure of concrete develops with the hydration of the cement into a hard, sponge-like structure. When we make concrete in a lab, everything takes place at a controlled temperature of 73 F. However, it’s impossible to control the weather on a job site. The best you can do is anticipate what might happen and be ready to respond accordingly.
When concrete cures at elevated temperatures, it’s stronger at 1 day but weaker at 28 days. Let’s say a concrete mixture has a 1-day compressive strength of 500 psi if it cures at 60 F. That same mixture cured at 120 F could have a 1-day strength of 2200 psi. But at 28 days it’s quite a different story. The concrete cured at 60 F has a strength of 5800 psi, while the same concrete cured at 120 F has a strength of only 4200 psi.
Back in the 1960s, Verbeck and Helmuth theorized that the difference in strengths stems from a difference in microstructure. They noted that while high temperatures accelerate both diffusion and hydration of cement, the rate of hydration increases more. That is, when the cement dissolves, it hydrates quickly, before it can diffuse very far from the original cement grain. That leaves dense shells of hydration products near the cement grains and an open pore structure between them. Optical microscopes can’t show structures this small, so they couldn’t verify their theory at the time.
Electron microscopes give a different view
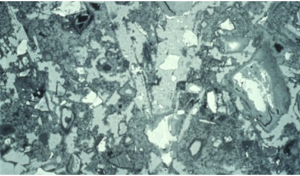
Twenty years later, researchers in Norway used backscattered electron imaging to examine cement pastes cured at 20 and 70 C (68 and 158 F) to the same degree of hydration. Backscattered electron images show relative densities. The densest materials are white, the less dense materials various shades of gray, and the pores are black. As you can see in the images, when the cement hydrates at 20 C, the pores are relatively small and unconnected.
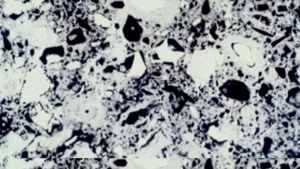
On the other hand, curing at 70 C produces a very different structure. There are dense shells of hydration products around the cement grains and large, interconnected pores in between. Exactly as Verbeck and Helmuth predicted, the large pores make for a weaker material.
Generally speaking, when we want high-performance concrete we care more about properties other than strength. For example, we may want the concrete to be durable in a harsh environment. Usually that means we want it to resist penetration by water, chloride ions, or other harmful materials. In tests of chloride ion penetration of concrete, raising the curing temperature from 20 to 50 C was equivalent to raising the water-cement ratio from 0.40 to 0.58. No one would expect concrete with a 0.58 water-cement ratio to be durable.
How to get good performance when concrete cures at elevated temperatures
Mehta and Gerwick observed that the steam-cured precast concrete beams in the San Mateo-Hayward Bridge over the San Francisco Bay in California exhibited such extensive corrosion that they required repairs. Cast-in-place beams made from similar concrete performed well in the same bridge.
If you were making concrete in a lab, you might cure it at a low temperature for a long time to get the best result. But that’s not practical for real concrete. In the field you don’t have that much control over the curing temperature. There are things you can do to keep the temperature within reason, but there are limits. And even if you could control the temperature, you can’t wait for weeks to remove the forms or open the pavement to traffic. How can you get good results when concrete cures at elevated temperatures?
This is where supplementary cementitious materials such as fly ash and slag cement can help. They’re less susceptible to ill effects when concrete cures at elevated temperatures. For example, combinations of slag cement and silica fume made steam-cured concrete far more resistant to chloride ion penetration as measured by ASTM C1202. Concretes with the same water-cementitious materials ratio rated from 11,000 down to 200 coulombs–all because of the selection of cementitious materials.
In conclusion, when concrete must cure at elevated temperatures, consider what you want. To compensate for lower strength, reduce the water-cement ratio. To compensate for the increased permeability, use supplementary cementitious materials. However, even with supplementary cementitious materials, the concrete will still experience negative effects. It’s worth optimizing the mixture proportions to get the best result. Beton can help you get the results you need.