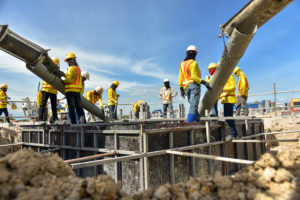
For quality assurance in concrete construction, the most common acceptance criterion is the compressive strength of the concrete. A field technician makes specimens according to ASTM C31, Standard Practice for Making and Curing Concrete Test Specimens in the Field. Within 48 hours, the specimens are transported to the lab. A lab technician tests them in accordance with ASTM C39, Standard Test Method for Compressive Strength of Cylindrical Concrete Specimens.
The strength of standard-cured cylinders does not represent the in-place strength of the concrete in the structure, but it serves as the basis for judging the adequacy of concrete delivered to the project.—Obla et al., 2018
Get the best lab, not the cheapest one
The lab acts as the arbiter between owner and contractor. A trustworthy lab maintains the balance between the owner’s risk of accepting bad concrete and the producer’s risk of rejecting good concrete.
If a test shows that the concrete doesn’t meet the specification, the Engineer of Record must determine what to do. Usually that entails additional testing, which takes time. In the end, the Engineer must decide whether the strength is acceptable. If not, removing and replacing the defective concrete affects both cost and schedule.
In concrete strength testing, just about any error will produce an artificially low result. These tests are relatively simple and don’t require major capital investment. In most places it’s easy to find someone to perform them cheaply. But doing it consistently right matters, and that’s neither easy nor inexpensive. ASTM C1077 spells out how to evaluate laboratories doing the testing. We’ll discuss the cost of bad testing in a future blog. But first let’s look at how to do it right.
ASTM C31 personnel requirements
Who performs the tests? Both the lab and the individual technicians must meet the requirements of ASTM C1077, Standard Practice for Agencies Testing Concrete and Concrete Aggregates for Use in Construction and Criteria for Testing Agency Evaluation. The technical director must be a professional engineer with at least 5 years’ experience in construction materials testing. Lab- and field supervisors must have at least 3 years’ relevant experience, along with certifications in the tests they supervise. Technicians must have the relevant certifications as well. Certification bodies list current certifications on their websites, so it’s easy to verify the lab and the technicians.
The field technician samples the concrete from the truck and mixes it in a wheelbarrow to make sure it’s uniform. Then he or she measures the slump, air content, and temperature and casts cylinders for later testing. A test is the mean of two 6 x 12-in. cylinders or three 4 x 8-in. cylinders.
ASTM C31 curing requirements
For up to 48 hours, the cylinders remain on site. During that time they must be protected from direct sun and moisture loss. The temperature must remain between 60 and 80 ˚F (68 and 78 ˚F for strengths of 6000 psi or higher). A min/max thermometer records the temperature range, which should be on the lab report. We’ve discussed previously how high-temperature curing adversely affects the strength of concrete. Low temperatures slow the rate of strength gain, and freezing at early ages causes permanent damage.
After a day or two on site, the cylinders are still vulnerable to damage, especially if the concrete contains fly ash or slag cement. These materials promote strength and durability at later ages, but gain strength slowly at first. They are also more sensitive to cold weather. Rough handling and transport could induce cracking, which will weaken the specimens.
Initial curing on site
How bad is it if the initial curing doesn’t conform to ASTM C31? Obla et al. report that a 1-day cure at 37 ˚F and 100% RH did not affect the 28-day compressive strength. However, the concrete would be easy to damage in handling and transport. Initial curing at 73 ˚F and 60% RH resulted in about a 10% loss of strength. One day at 100 ˚F and 25% RH reduced the strength by 12%; 3 days reduced it 18%. In a study of jobsite practices, initial curing conformed to ASTM C31 about half the time.
Contracts and specifications don’t always make clear who is responsible for initial curing. The testing agency can provide the containers and min/max thermometers, but will need a supply of water and a secure location for storage. Insulated containers such as ice chests filled with water may be sufficient. Use cool water (with ice if necessary) in summer and warm water in winter. In some cases electricity is necessary to maintain the temperature. The specimens also need protection from direct sun. When the contract spells out requirements and responsibilities, it’s easy to include curing in the project budget. If not, you can expect deficient curing and low strength tests.
Troubleshooting
Tracking and reporting the temperature range for the initial cure are essential. In a previous job, I investigated every concrete strength test result that didn’t meet the specification. The first thing I looked for was full conformance to ASTM C31 and C39. Because initial curing can be hard to control, it often explained the shortfall. Typically, curing temperatures would be too high in August, and the test results would be lower then than the rest of the year.
In the lab
ASTM C31 requires that within 30 minutes of removal from their molds, the specimens remain at 73.5 ˚F with free water on their surfaces until they reach the testing age.
ASTM C39 specifies how to test the cylinders for compressive strength. The lab technician must have proper certification and supervision. ASTM C39 prescribes such test conditions as alignment of the specimen, rate of loading, calculations, and reporting.
The report should include the diameter and cross-sectional area of the cylinder, maximum load, compressive strength, and type of fracture. If the fracture isn’t symmetrical, it means that the loading wasn’t symmetrical. That will yield an artificially low test result. The ends must be smooth and flat so the load is applied evenly to the whole surface. Either grinding or capping with an appropriate material is necessary. The technician should note any visible defects in the cylinder or the cap. These, too, can lower the test result.
Quality assurance data include running averages of the strength tests over time. This type of analysis smooths out the variations to show overall trends. Lab technicians don’t always load specimens to failure, instead stopping the test once the load exceeds the requirement. While this practice assures that the concrete is acceptable, it distorts the data. In particular, it makes it impossible for the producer to know when the concrete is too strong. That is, it addresses the owner’s risk but not the producer’s risk.
Compensating for poor testing
At the beginning of the job, the producer may add extra cement to ensure that the concrete meets strength. If the running average shows it’s more than enough, they may want to reduce the cement content. But they can’t do that without reliable data. Any deviations from ASTM C31 and ASTM C39 will make the results artificially low. Stopping the test before failure adds to the producer’s costs, which they must pass on to the owner. We’ll discuss the economic and environmental costs of overdesign in a future blog.
Getting on the same page
The National Ready Mixed Concrete Association has developed a preconstruction checklist to make sure acceptance testing conforms to ASTM C31 and C39. The Engineer of Record, contractor, concrete producer, and testing agency can use this checklist as a guide in their pre-construction meeting. They can discuss the details of how the testing will be conducted, who is responsible for what, and who has what authority. Hashing out these details ahead of time helps prevent disputes and resolve any problems that crop up. ACI PRC 132.1 spells out the responsibilities of the various parties on the project to help the job go more smoothly.