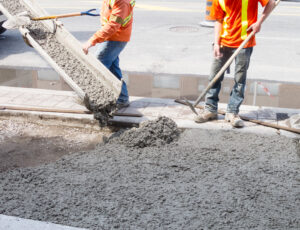
Acceptance of concrete delivered to the job site is usually on the basis of compressive strength tests in accordance with ASTM C31 and ASTM C39. To compensate for variability in the concrete itself and in the testing, concrete producers proportion their mixtures for a higher average strength than the specification calls for. Some overdesign is necessary. However, excessive overdesign is costly in both economic and environmental terms.
Prescriptive and performance specifications
ACI 301 has two requirements for concrete compressive strength:
- Every average of three consecutive tests equals or exceeds the specified strength, fc’.
- No test falls below fc’ by more than 500 psi if fc’ is 5000 psi or less, or by more than 0.10fc’ if fc’ exceeds 5000 psi.
If there are at least 30 tests of the same concrete, the necessary overdesign depends on the standard deviation of the test results. The higher the standard deviation, the higher the target strength needs to be. That is, the better the quality control the lower the target strength. The statistical criterion is a performance requirement.
Some specifications prescribe a value for the overdesign. ACI 301 provides such values when there aren’t enough data to use the statistical approach. For example, when the specified strength is between 3000 and 5000 psi, the target strength is 1200 psi above the specified strength. Once enough data are available, the producer can reduce the target strength accordingly. Maintaining this prescriptive value throughout the project would result in undue overdesign. That would be the case if the 1200-psi margin were fixed.
Another common prescriptive requirement is a minimum cement content. If the concrete could achieve all the necessary performance characteristics at a lower cement content, any excess cement is a waste of money. It also unnecessarily increases the project’s carbon footprint.
Such prescriptive requirements reduce the incentive for the concrete producer to exercise quality control measures. That is, the prescriptive approach is a perverse incentive—discouraging the producer from doing something desirable. Quality control—everything the producer does to ensure that the concrete meets the specifications—is expensive. If they have to use more cement than necessary anyway, why should they go to the additional expense of better quality control?
How consistent is the testing?
Even the best concrete will have a hard time passing inconsistent or poorly executed tests. As we’ve discussed in a previous blog, just about any deviation from the standard procedures of ASTM C31 and C39 will yield artificially low test results.
Quality control is expensive for the laboratory as well as for the concrete producer. To make sure the testing consistently conforms to ASTM C31 and C39, the laboratory manager must foster a culture of continuous improvement. The technicians must obtain and maintain certification by ACI, their state DOT, or some other agency. In addition, all of the testing equipment must be maintained and calibrated. Test specimens must receive appropriate curing and handling from fabrication through testing. As a check, an agency such as CCRL must inspect the laboratory, verify the calibration of equipment, and ensure that the technicians are conducting the tests correctly.
Naturally it’s easier to keep track of practices in the laboratory than in the field. But in their first 24 to 48 hours, the specimens are most vulnerable to damage and the effects of improper curing. Our colleague, Julie Buffenbarger, and her coauthors reported on a survey of 103 construction projects. All of these projects were under the jurisdiction of the Pennsylvania Uniform Construction Code. The survey showed that the specimens received proper initial curing on only 21 of these projects. That is, on four projects out of five, the test specimens got no curing or improper curing. The authors pointed out that improper fabrication and curing can reduce concrete strength by up to 61%. Overall, the survey showed proper adherence to ASTM C31 and C39 on only 15 out of the 103 projects. ACI PRC 132.1, which lays out the responsibilities of the respective parties in a construction project, offers a better approach.
What are the implications for overdesign?
If only 15% of the projects experienced proper testing, that means that the test results for the other 85% of the projects were biased low. That is, the producer’s risk of rejection of good concrete was artificially high because of poor testing practices. Every time the compressive strength fails to meet the specification, work stops until the Engineer of Record determines what to do. Can this particular member perform adequately at the lower strength? Do they need to take cores to see whether the concrete has reached strength after all? Can they reinforce the member to make it stronger, or is removal and replacement the only acceptable remedy?
Whatever they decide to do, the delay itself is expensive. Many construction contracts provide for liquidated damages. That is, the contract spells out the cost of each day’s delay beyond the completion date. To avoid having to pay them—and the costs of any remedial measures—the concrete supplier targets a higher strength.
But what if, as the Pennsylvania study indicates, improper testing is effectively the standard of care? The concrete producer has no control over who does the testing or how well they do it. They can only increase their target strength and hope it’s high enough to pass.