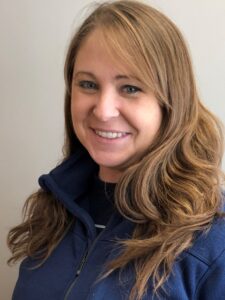
Heidi Lukkarila, Beton’s field technician, has many years’ experience troubleshooting concrete on the jobsite. Troubleshooting requires the ability to think on your feet, as time is always of the essence. Here are a few of her more memorable experiences.
Hockey rink
Placing concrete for a hockey rink is complex because of all the inclusions—not only reinforcing bars, but also cooling pipes. In this case, the concrete was going to be pumped; it also needed to flow into place and consolidate around the inclusions.
We’ve discussed the importance of the pre-pour meeting. NRMCA has even developed a preconstruction checklist to set the agenda. Unfortunately, a series of miscommunications meant that neither Heidi nor the batchman had participated in the pre-pour meeting. They hadn’t heard how far they were pumping the concrete or whether they were using a rubber hose or a rigid pipe. And they hadn’t done any trial batching.
The salesman had thought a 9-inch slump would do the trick, but what they really needed was self-consolidating concrete. It’s not possible to adjust one to make the other. Self-consolidating concrete requires not just the right combination of admixtures, but attention to the aggregate grading and all the other mixture parameters. Heidi had to do the best she could by making adjustments on site.
In a project like this, adjustments are also necessary as the pumping proceeds. The crew pumps the concrete to the farthest locations first, then removes some of the line. With a shorter pumping distance, there’s less slump loss, so you need less water reducer. And to get the concrete to set at about the same time, you also decrease the amount of retarder. That way the finishers can finish the whole surface at the same time.
Heidi notes that it’s important to pay attention to what people need. If the finishers appear to be struggling, she’ll ask them how it’s going and make adjustments to the concrete to make it easier for them. Despite the rough start, she was able to make it all work.
Equipment breakdown
On another project, the contractor had to delay the placement because their screed wasn’t working. He’d forgotten to notify the concrete plant, so Heidi had 70 yards on site ready to place. They needed 30 to 45 minutes to get the screed up and running before they could place the concrete. Heidi used the trucks’ temperature probes to monitor when the concrete was starting to set. Any time she noticed the temperature rising, she’d dose that load with retarder to buy more time. The contractor had to move quickly, but they were able to finish the placement without excessive retardation—or wasting all that concrete.
The torque on a mixer truck will also indicate when the concrete is starting to set, but it’s a lagging indicator. Temperature gave her the information she needed in time to prevent problems.
Troubleshooting the air-void system
Concrete that undergoes cycles of freezing and thawing needs a good air-void system for durability. To get that, we add an air-entraining admixture, which is a surfactant. Water reducers and shrinkage-reducing admixtures are also surfactants. These admixtures can interact with one another, so it’s important to adjust the batching and mixing to get a good result.
If you’re supplying a job from more than one plant, you’ll see different results from the same mixture. The mixer in one plant may be faster or more efficient than another, so you may need to adjust the timing of your admixture additions.
On one project, the concrete supplier was using two different plants about the same distance from the jobsite. The concrete from one plant was losing about 1% air between the plant and the site, while the other one was gaining about 1%. The concrete contained a shrinkage-reducing admixture, which reduces the surface tension of the water. It can also reduce the air content, so it may be necessary to add the air-entraining admixture afterwards. In this case, she found that adding the air 5 minutes after the shrinkage-reducing admixture got them close to what they wanted. Then at the site they’d check the air and add more air-entraining admixture if necessary.
The performance of air-entraining admixtures also depends on the temperature of the concrete. We’ve discussed concreting in hot- and cold weather. Air entrainment is more difficult in hot weather, but even diurnal temperature changes can affect how air-entraining admixtures perform. It’s important to monitor the concrete temperature. You may have to adjust the amount of hot water in the mixture. Keep in mind that materials that have been sitting outside in cold weather will behave differently from material that was warm inside the plant overnight.