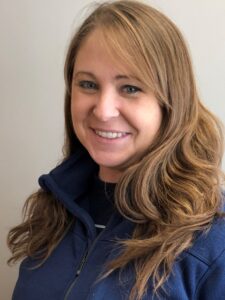
Heidi Lukkarila is Beton’s new field technician and nondestructive testing specialist. She comes to us with 12 years of experience in field testing and troubleshooting concrete mixtures. She’s worked with construction foremen, finishers, ready-mix concrete producers, and architects to obtain the performance they need from the concrete and make sure it complies with the specifications.
How did you do troubleshooting in the field?
I was responsible for high-performance concrete placements in the south metro of the Twin Cities. These days, concrete mixtures are so complex that it can be hard to sort out what’s causing the problem. Years ago, concrete was basically just cement, water, coarse and fine aggregate, and maybe an admixture or two. Now, though, you’ll have several types of water reducers, maybe a VMA*, a corrosion inhibitor, and more. You’ll usually have two or three cementitious materials, so you’ll have many possible chemical interactions.
The flow of fresh concrete depends not only on the admixtures, but also on the grading of the aggregates. We used to batch aggregates in two fractions—fine and coarse—but now we have at least three for better control of the grading. Some people think that because aggregates are chemically inert, they don’t affect the properties of the concrete. But aggregate grading has a huge effect on workability and finishing characteristics.
A lot of what I know about troubleshooting is based on experience with how aggregate grading affects flow and how the various admixtures interact. I look at how the concrete behaves in the truck and add admixture until it looks like a bit too much, then add a couple more “glugs”.
How have you used admixtures to get the performance you want?
On one job the customer needed the concrete to flow through the forms without any internal vibration. Ideally we would have used self-consolidating concrete, but there wasn’t time to do the additional mockups we’d have to do. So I increased the dosage of superplasticizer and added VMA to help it flow and keep it consistent. We still needed some external vibration to get it to consolidate. But when the forms were removed, there was no honeycombing.
On another project, a warehouse floor, the slab kept tearing as the finishers were working on it. It was a winter placement, so the ready-mix producer was using some hot water in the concrete, and the warehouse was heated. We needed to slow the reaction so the concrete wouldn’t set too quickly. I added a slump stabilizer—a time-release superplasticizer. That made the concrete easier to place, and the finishers had time to close the surface. The foreman told me the next day that they achieved the highest flatness score he’d seen in his 30-year career—almost a super flat floor. That showed him he could bid on super flat floors in future projects.
I understand you’ve worked with architectural precast concrete. What was that like?
To maintain the consistent appearance people expect from architectural precast, you need to maintain tight control of the materials. Also, the order of batching is important, especially when you’re working with powdered pigments. You have to mix it thoroughly so the color is evenly distributed throughout the concrete. I worked with exposed aggregate finishes. In that application, the color can appear uneven if some areas have more exposed aggregate than others. I inspected the placement of the rebar in the forms to make sure there was enough cover. With thin panels, rebar too close to the surface can cast shadows you can see on the surface. I also inspected the panels afterwards. When we did mockups, I’d go with the architect to check them. That way I could better understand their vision of the finished product.
Can you tell us about an unusual job you worked on?
One time we were supplying the same fiber-reinforced concrete mixture from two different plants. On the way to the jobsite, the concrete from one plant was losing air content, while the concrete from the other plant was gaining air. It turned out the problem was the fibers. They’re processed with a solution that has to be washed off. The two plants were working with different lots of the same fiber. One lot still had residue from the processing solution, and that was entraining air in the concrete. You really have to look at everything to figure out what’s going on.
As you can see, Heidi Lukkarila has a lot of practical knowledge that will serve our clients well. Join us in welcoming her to Beton.
*Viscosity-modifying admixture