Engineering has always been about the wise use of resources. Traditionally, the profession focused on resources in the microeconomic sense. That is, the economic interests of the owner, employer, or client were paramount. Over the last few decades, however, engineers have had to think more broadly about whose interests are of concern and what resources to consider. With climate change and diminishing resources, sustainability has become an integral part of good engineering.
Cement and concrete
In our industry we talk about reducing the carbon footprint of concrete or of cement. But is that the best approach?
Portland cement manufacture generates CO2 from clinkering, breakdown of limestone (CaCO3), and grinding. Cement manufacturers have reduced the carbon footprint of clinkering and grinding. But the only way to reduce CO2 from the breakdown of limestone is to reduce the portland cement content. Cement companies do that by blending in materials such as limestone, fly ash, slag cement, silica fume, and calcined clay. But so long as the cement contains portland cement clinker, its carbon footprint is not zero.
Most of the carbon footprint of concrete is due to cement, so we need to reduce the cement content. Ways to do that include more efficient aggregate grading, judicious use of water reducers, and avoiding overdesign. Still, less carbon is not zero.
Zero-carbon concrete can’t incorporate portland cement. Geopolymers made without portland cement are in development. They behave differently from portland cement, though, necessitating changes in practice. Because they are less reactive, we either have to activate them or accept that setting and strength gain will take days, not hours.
Activation could be by heating, as we do now with precast concrete, or by adding alkalis. Naturally heating increases the carbon footprint. But the chemical option could prove hazardous to construction workers. Portland-cement concrete is highly alkaline (pH 12 to 13), but geopolymer mixtures could involve materials with pH as high as 15. On a jobsite, workers who get fresh concrete on their skin need to rinse it off within the hour. In contact with a pH of 15, their skin would saponify* immediately. They’d need more protective gear and different jobsite practices to stay safe.
Drawing the right boundaries
It’s important to think about where we draw the boundaries that define the problem. Suppose we consider not the ton of cement or the cubic yard of concrete, but the whole structure—the building, bridge, or pavement. In this case more clinker in the cement or more cement in the concrete may give us a lower carbon footprint overall. How does that work?
We may need more cement per cubic yard to give the concrete greater durability and/or higher strength. Let’s say we’re designing a bridge for a location in the upper Midwest. It will have to withstand cycles of freezing and thawing, deicing salts, and abrasion from snowplows. So we’ll need a relatively low water-cementitious materials ratio. That will give us a relatively high strength regardless of whether the structure requires it.
But if we design the bridge properly, we can take advantage of that high strength in several ways. We may want to prestress the girders to make the best use of the high compressive strength. That allows us to use fewer girders and/or have longer spans. Either way, we’ll need fewer piers to support the bridge. Also, the girders that support the deck could be lighter, so we won’t need such massive foundations. Efficient design of the structure results in less concrete, so even if there’s more cement per cubic yard, there are fewer cubic yards. That makes for a smaller carbon footprint overall. Accurate, reliable testing allows us to produce concrete more efficiently, without excessively high strength.
Durability is also an important aspect of sustainability. The longer a structure continues to serve its purpose, the less frequently it needs repair or replacement. Fortunately, it isn’t necessary to make tradeoffs between low carbon and durability. Appropriate use of supplementary cementitious materials can improve durability and other aspects of performance.
Carbon capture and absorption
The cement industry’s plan for net-zero-carbon concrete by 2050 includes carbon capture. The technology isn’t ready for implementation just yet.
However, concrete absorbs CO2 from the atmosphere in a process we call carbonation. Chemically, calcium hydroxide (a product of portland cement hydration) combines with CO2 to form CaCO3. This is just the reverse of the breakdown of limestone in clinkering. Carbonation leaves a hard, dense shell on the surface of the concrete. That shell impedes the diffusion of additional CO2 into the concrete. But if you were designing a pavement, you might plan on grinding the surface every 15 to 20 years in order to maintain a safe driving surface. That would expose fresh surface, renewing its ability to absorb CO2 from the air.
However, you need portland cement clinker in the concrete if you want it to absorb CO2. The cementitious materials that displace portland cement work by reacting with calcium hydroxide to form calcium silicate hydrate. Calcium hydroxide that has already reacted won’t be available to absorb CO2. In most cases you’re probably better off reducing the portland cement content and not counting on carbon absorption. The main thing, though, is to recognize that you have to choose; you can’t have both.
If you opt for carbonation, you also have to choose between now and later. If you use CO2 to cure concrete, that concrete is not going to be able to absorb CO2 over its service life unless you expose new surface.
On the other hand, let’s say you’re building a pavement. You could recycle concrete from an existing pavement to use as the base for your new pavement. That could be more economical than quarrying virgin aggregate. In addition, crushing the concrete to size will expose new surface that can absorb CO2.
Sustainability is good engineering for the St. Croix Crossing
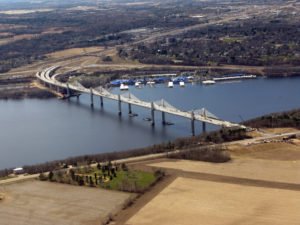
The St. Croix Crossing between Minnesota and Wisconsin illustrates how good engineering makes for sustainability. Supplementary cementitious materials substituted for 30% of the portland cement in the segments for the spans, reducing the carbon footprint accordingly. By engineering this concrete for durability, we also reduced the need for future maintenance and repair.
In the piers and other massive elements, only about 15% of the cementitious material is portland cement. This concrete took advantage of the lower heat evolution of supplementary cementitious materials to minimize thermal cracking. That is, good engineering promotes sustainability by reducing the carbon footprint while enhancing performance.
Sustainability is simply good engineering: optimizing resources, balancing competing interests, and making incremental improvements as knowledge improves.—Van Dam and Taylor, Concrete International
To minimize disruptions to the habitat of eagles, native plants, and aquatic life, the structural design limited the number of the piers and the heights of the towers. The resulting reductions in volume of concrete also reduced the carbon footprint.
*Transform into soap.